Electric Motors Condition Monitoring
Electric Motors Condition Monitoring
We can carry Condition Monitoring of Electric Motors both in on-line as well as off-line mode. The on-line methods are Vibration Analysis, Ultrasound Analysis and Thermography. The off-line methods are Winding Resistance Test, Inductance Test, Surge Comparison Test, Polarization Index Test, Insulation Resistance Test, High Voltage Test (for HT Motors), Tan Delta and Capacitance Test (for HT Motors only). The off-line test can be carried out only when the plant is taken under shutdown.
We can carry Condition Monitoring of Electric Motors both in on-line as well as off-line mode. The on-line methods are Vibration Analysis, Ultrasound Analysis and Thermography. The off-line methods are Winding Resistance Test, Inductance Test, Surge Comparison Test, Polarization Index Test, Insulation Resistance Test, High Voltage Test (for HT Motors), Tan Delta and Capacitance Test (for HT Motors only). The off-line test can be carried out only when the plant is taken under shutdown.
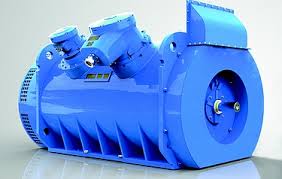
.jpg)
OUR PRODUCT:
1.On-line Condition Monitoring of Electric Motor with NDT Techniques:
As said earlier, on-line CM comprises of combination of Vibration Analysis, Ultrasound Analysis and Thermography.
i.Vibration Analysis on Electric Motor- The vibration readings will be taken on DE & NDE-sides of motor in axial, horizontal and vertical directions. The FFT data will also be taken with vibration measurements and then it is analyzed. Time waveform will be studied wherever necessary.
The vibration analysis of electric motor will tell us about bent shaft, misalignment, unbalance rotor, broken/cracked rotor bar, uneven gap between stator & rotor, faulty bearings, eccentric rotor, loose or deformed base rail, soft foot, mechanical looseness, etc. in motor.
ii.Ultrasound Analysis on Electric Motor – The major advantage of this testing is to know the condition of bearings and additionally we can know some other problems like stator-rotor rubbing, etc. (Ultrasound Analysis alongwith Vibration Analysis can give precise information about bearings.)
iii.Thermography of Electric Motor- Here we map the core of induction motor to know about winding overheating and we map the bearings for any anomalies in it.
With the combination of these three NDT methods, we can precisely conclude on the condition of the motor. The anomalies those are not detected by one of the method are detected by another method, and hence these methods are compensating each other when carried out together.
2.Off-line Condition Monitoring of Electric Motor :
These inspections are only possible when the plant is under shutdown.
1.On-line Condition Monitoring of Electric Motor with NDT Techniques:
As said earlier, on-line CM comprises of combination of Vibration Analysis, Ultrasound Analysis and Thermography.
i.Vibration Analysis on Electric Motor- The vibration readings will be taken on DE & NDE-sides of motor in axial, horizontal and vertical directions. The FFT data will also be taken with vibration measurements and then it is analyzed. Time waveform will be studied wherever necessary.
The vibration analysis of electric motor will tell us about bent shaft, misalignment, unbalance rotor, broken/cracked rotor bar, uneven gap between stator & rotor, faulty bearings, eccentric rotor, loose or deformed base rail, soft foot, mechanical looseness, etc. in motor.
ii.Ultrasound Analysis on Electric Motor – The major advantage of this testing is to know the condition of bearings and additionally we can know some other problems like stator-rotor rubbing, etc. (Ultrasound Analysis alongwith Vibration Analysis can give precise information about bearings.)
iii.Thermography of Electric Motor- Here we map the core of induction motor to know about winding overheating and we map the bearings for any anomalies in it.
With the combination of these three NDT methods, we can precisely conclude on the condition of the motor. The anomalies those are not detected by one of the method are detected by another method, and hence these methods are compensating each other when carried out together.
2.Off-line Condition Monitoring of Electric Motor :
These inspections are only possible when the plant is under shutdown.
-
We begin with Winding Resistance / Inductance Testing to check resistance / inductance imbalance in phases of winding.
-
Surge Comparison Test is conducted to check for interturn short, if any.
-
Polarization Index Test and Insulation Resistance Test is conducted to check the quality of insulation.
-
High Voltage Test is conducted only on HV Motors (3.3kv, 6.6kv, 11kv) to check the strength of the insulation of the winding.
-
Tan Delta and Capacitance Test is conducted only on HV Motors (3.3kv, 6.6kv, 11kv) to know the quality of insulation, contamination in insulation, ageing of insulation, etc.
This off-line testing gives us a clear picture about the condition of the windings and hence needs to be conducted twice or once in a year whenever the pre-planned shutdown of plant is scheduled. It is not necessary to conduct it more frequently.
Procedure:
On-line Condition Monitoring of Electric Motor –
Procedure:
On-line Condition Monitoring of Electric Motor –
A. Base Data Generation - Under this, we generate ‘BASE DATA’ of all the given electric motors through Vibration Analysis, Thermal Mapping, and Ultrasound Analysis.
a) Base Data through Vibration Analysis – We not only carry Vibration Measurements but we do Vibration Analysis on given electric motor and the base data includes,
-
Vibration FFT analysis – the data is captured setting the range of measurement looking at Fundamental Frequency (motor rpm – 1 x) and its harmonics (2x, 3x, 4x etc). The Waveforms and analysis report is maintained as base data.
-
Vibration Time Analysis (Optional) – The time waveform is captured along with FFT, analyzed and kept in record as base data.
-
Vibration Measurement Readings taken at Vertical, Horizontal, and Axial direction of the electric motor under CM.
Here the points of measurement on electric motor are marked permanently and the instrument used is noted down. And the measurement is taken on same marked points with same instrument during next all measurements of condition monitoring.
b) Base Data through Ultrasound Analysis – The Points are marked on bearing housing (permanent) and the ultrasound readings are taken at that point. The Peak, RMS values of ultrasound and the crest factor is recorded. The graph is saved. This data will then be compared with further measurements taken under CM program.
c) Base Data through Thermography –
The bearing and core is mapped thermally from specific defined distance and angle. The distance and angle is noted down in the data. The thermogram is saved to compare with further thermograms those will be taken during CM program.
Important: We might locate any fault in any motor during this survey of base data generation. In that case, we request/ suggest customer to repair the fault/ take corrective action in that motor. The data is taken again after corrective action. And the data taken after corrective action will be recorded as ‘Base Data’ of that motor.
Important: We might locate any fault in any motor during this survey of base data generation. In that case, we request/ suggest customer to repair the fault/ take corrective action in that motor. The data is taken again after corrective action. And the data taken after corrective action will be recorded as ‘Base Data’ of that motor.
B. Condition Monitoring Visits, Trend Analysis (All visits after Base Data generation)
-
After Base Data generation, depend on conditions of electric motor, the frequency of condition monitoring visits for particular motor will be scheduled. (This means for the motors under higher risk, higher frequency of visits will be scheduled, say weekly/fortnightly and for motors having lower risk, lesser CM visits will be scheduled.) This schedule can be changed time by time for particular motor, after correction or after developing fault in it.
-
Visits for condition monitoring will be made as per scheduled program.
-
When ever found any anomalies in any motor during monitoring, will be immediately informed to customer and mentioned in record/ report with suggestion of corrective action.
-
Trend Analysis: After every CM visit, the readings, / measurements of VA, UA & IR are taken in trend analysis. The report of trend analysis will be given after 3rd CM visit onwards, with CM visit report.
![]() |
![]() |
Preface:
Among the motor failures, 60% of the failures are because of bearing failures, 30% are because of winding problems and remaining 10% are because of some other problems. There are many reasons for bearing failure as well as winding failures. If we monitor bearings and windings & take timely corrective actions, we can make sure flawless service from the motor.
The on-line NDT methods like vibration and ultrasound analysis eliminate the reasons causing bearing failure. Many times a simple bearing failure turns into a catastrophic failure of the motor. In that case, the stator gets rubbed with the rotor and hence it damages the stator core, rotor core, rotor winding and stator winding. Hence we can secure motor from catastrophic failure if we take care of the bearing.
Windings can be monitored through off-line inspections and if we add preventive measures (overhauling of the windings) in it, we can secure the motors from anomalies and can get flawless performance of the motor.